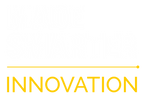
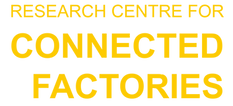
Background

The image above demonstrates some of the key problems and the current state of many manufacturing supply chains. Many problems such as managing disruptions of changes in production volume impact not just a single manufacturer of a single site but impact multiple manufacturing sites and companies within a supply chain. Coordination and collaboration is needed between multiple sites and companies to address these challenges in a robust and effective way.
​
Over the last 20 years many smart manufacturing demonstrators have been created to aid research into and show the benefit of new technologies for manufacturing. Our reviews of these demonstrators have highlighted several shortcomings not yet addressed:
​
-
Demonstrators focus on a single production line or machine. No smart factory demonstrators focus on coordination between companies and sites and very few even focuses on a whole company. This means they fail to take account of the complexity of addressing these problems. ​
-
Demonstrators often only produce a single product in batches of one. This is not representative of a manufacturer who may be producing hundreds or thousands or products in a day. ​
-
Legacy equipment is often not used or integrated effectively. There is a tendency to use new equipment with state-of-the-art capabilities. Most companies do not have this equipment.
Demonstrator
The VOOM demonstrator aims to replicate an intelligent production flow utilising multiple labs across the Institute for Manufacturing, with each acting as individual interacting factory sites in a single or multi-site company or a supply chain. Key functions include adaptive robotic assembly, augmented reality training, and machine learning-supported 3D printing production. The key research aims of the demonstrator are:
​
-
​Flow coordination: Create a coordinated production flow able to change location, volume, mix and production resources to deal with different scenarios. ​
-
Data sharing: Investigate how the degree of data sharing between companies, facilities or labs impacts the ability to respond to possibly detrimental scenarios or challenges. ​
-
Adaptation: Investigate data that can be used within and between production facilities or companies to respond to different scenarios. ​
-
Low-cost solutions: Integrate novel low-cost solutions to support production distributed across multiple “connected factories”.
​
The image below shows an example of the flow of parts between each lab acting as a factory.

Use of Demonstrator
The demonstrator has been used in several research activities already. These activities include:
-
Testing and comparing data sharing methods between factories using QR codes, cloud servers and email.​
-
Validations and testing of low-cost digital solutions for monitoring utilisation and recording production cost.​
-
Testing of low-cost PLC monitoring solutions during production operation.​
-
Tests of machine learning error correction and AR assembly guidance during production operations. ​
-
Communication of production delays between manufacturers in different sites.